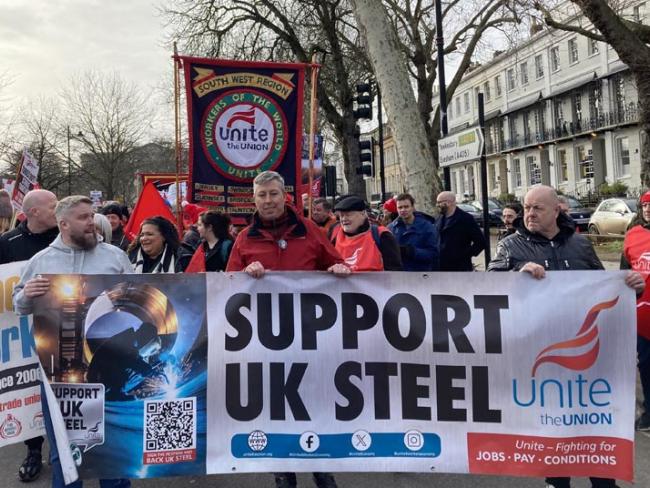
Cheltenham, January: marching for steel in the face of threats to close the furnaces at Tata Steel, Port Talbot. Photo Workers.
Steel is vital for manufacturing and infrastructure. Producing it is energy intensive, but closing blast furnaces without a realistic plan for future steel production undermines Britain’s self-reliance...
Steel is a key material for the economy and industries of any country. It is used in buildings, ships, railways, vehicles, packaging and machinery of all sorts. No advanced industrial country except Britain considers moving away from producing virgin steel.
Any plan for a transition to electricity as our main source of energy must embrace the role of steel. It is used in many ways for electricity generation and transmission – in transformers, cables and pylons. There will be no green revolution without steel.
The first question is whether Britain needs to make steel at all – can we not just buy it? The answer is “no” – abandoning security of supply and relying on imports for such a vital material is a risk to our independence.
Can we not just recycle scrap steel instead? Virgin steel – made from raw materials – is essential for some applications. And even opponents of steel making in Britain accept that at least 20 per cent of our steel usage (currently 15 million tonnes a year) would not come from recycled steel.
Exporting
The statistics on recycling make interesting reading. Britain creates around 10 million tonnes a year of scrap steel. But most is exported to be processed elsewhere. Our net need for steel of all types is 5 million tonnes a year, but by exporting 8 million tonnes of scrap, we need 13 million tonnes.
About 7 million tonnes of steel is made here each year. That uses just under 3 million tonnes of scrap – half of which is fed to blast furnaces producing virgin steel. The other half is processed by electric arc furnaces. These use electrolysis: putting electrodes into scrap metal to melt at high temperatures instead of smelting to turn iron ore into molten iron for primary steelmaking.
The demand, in the name of reducing emissions, to ditch blast furnace production is short-sighted – a recipe for destroying the whole industry.
Presently the two main processes for making steel are integrated and interdependent. Both are energy intensive, to different degrees – a shift towards electric arc production is possible (especially if
we exported less of the scrap produced). But those benefits depend on a supply of electricity.
The government has chosen to side with Tata by paying it £500 million to cut jobs and close blast furnaces. But there’s no guarantee for the future of what remains without a fight from workers – starting with those involved and the industries that depend on steel.
Workers at Port Talbot want the government to take a stake in the industry and not pay companies to shut it down. The GMB and Community unions at Tata Steel, together with Unite, presented their multi-union plan on 17 November last year.
Vulnerable
The plan expressed fears that a simple 3 metric tonne EAF would lock them into a single technological approach. They feared the loss of many jobs. And what’s left would be vulnerable as less green than its competitors.
Attempting to take responsibility for the direction of their industry in the face of global pressure to decarbonise, their proposal sensibly allowed for Blast Furnace No 4 to continue to the end of its life-cycle in 2032, while one small EAF would be constructed, and later a second.
This plan also envisaged using Direct Iron Reduction (DIR) in future. Taken altogether it would fully decarbonise steelmaking in time, as well as ensuring Britain retained a strategic ability to produce virgin steel.
The Materials Processing Institute, a research and development centre based on Teesside, gave the unions’ plan an unequivocal commendation. Stephen Kinnock, MP for Aberavon, called it “compelling”.
But the three unions are not in agreement. Unite subsequently went its own way and withdrew from the joint plan. It unveiled its own grand plan, “To transform the UK into the global green steel capital”. It called for new procurement legislation – for all infrastructure projects to use British steel.
That’s a good approach on supporting home produced steel. But in calling for the industry to be rebuilt Unite should clarify how it reconciles its emphasis on investment in green steel (produced by arc furnaces) with its declared opposition to blast furnace closures and the loss of jobs.
This difference must be resolved quickly. Divisions between unions will hinder the campaign for the future of the industry.
Pure steel is needed for the new technological age, but extracting it is a dirty business, energy and labour intensive. It does not come out of the ground all nice and shiny. It is an alloy of iron and carbon – impurities have to be removed before steel is made. Different steels depend on exact control of added metals.
Nor is it always possible to produce what we need. Generally speaking, high grade haematite (the most common iron ore) must be upwards of 65 per cent iron content. British ores are now mostly depleted and of poor quality; significant imports were from Norway and the USA in 2023.
Demand
There is still demand abroad for low-grade British ores. But on 6 November, Chinese-owned British Steel announced the closure of blast furnaces at Scunthorpe, with 2,000 redundancies. It was the latest in a long line of attacks on British industry. Sheffield steel had already been reduced to workshop-based niche products.
‘The demand to ditch blast furnace production in the name of reducing emissions is short-sighted – and a recipe for destroying the whole industry…’
Steel was to return in a different guise, as “green steel”, infinitely recyclable without loss of quality, so it is said, via electric arc furnaces. But the claim that recycled steel produced in this way is of consistently high quality is not entirely true: it cannot be used, for example, in certain parts of automobiles.
Electric vehicles require high grade steel, as does shipping. Recycled steel is vital to the automotive and manufacturing sectors: most cars have frames with 25 per cent recycled pure steel.
A single arc furnace requires a workforce of only 250. Labour MP Andy McDonald told local people – thousands of whom had lost their jobs – to embrace the change and “all that goes with it”.
The environmental argument goes that grid-based emissions can be drastically reduced through renewable electricity. Unite the Union spokesman Pat McCourt chose to emphasise the environmental aspect when he said, “What we need to see is a transition from carbon-producing, intensive steelmaking to utilising green energy to produce green steel”.
Businesses and local people on Teesside joined with Unite to demand not only more investment in green steel but also greater use of British-made steel in public buildings.
There are hopeful signs. For example, the South Korean manufacturer SeAH is using British steel to build its offshore wind turbine factory at Teesworks. The plant is expected to produce up to 150 monopiles (foundations) a year for installation in the North Sea.
Steel is a national staple, a national necessity. All other industrial production depends on it one way or another. Outsourcing its production to countries where carbon emissions are not so tightly controlled does nothing to reduce global emissions.