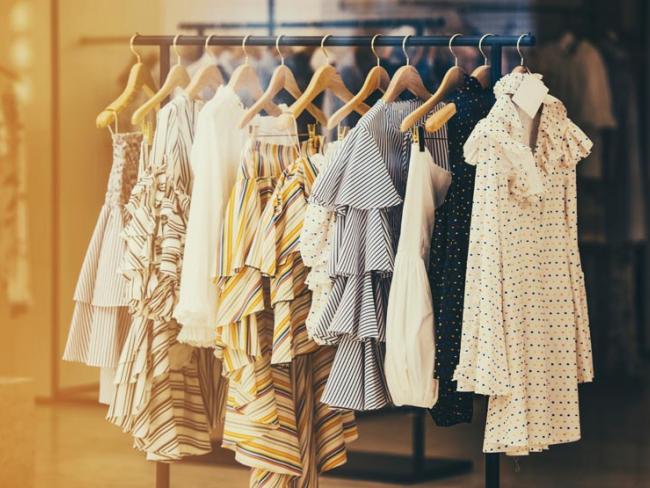
Clothing on a rack in a London store. It should be made here. Photo Creative Lab/shutterstock.com.
Experiences during the Covid pandemic plus new technologies could help rebuild the clothing industry…
Fashion House Boohoo’s announcement at the end of July that it is to set up its own factory in Leicester (see News, page 5) to make its own clothes has thrown the spotlight on the possibilities for the British fashion and textile industry after Brexit at the end of this year.
A number of brands are now looking at the advantages of local supply. Rather than have their clothes made in, say, Southeast Asia, they are now scrutinising the full costs involved in long supply chains.
We could – at last – be seeing a return to the days when retailers had their own factories, bringing employment back to Britain.
It’s a development being tracked eagerly by Katie Hills, whose website Make It British has been a powerful voice calling for the government to source its PPE clothing in Britain. And as a live podcast at the end of July showed, experiences with Covid are pointing the way to how to future-proof Britain’s textile industry.
When Covid hit in the early part of the year, Hills was instrumental in putting together a group of textile companies ready and willing to meet demand for the protective equipment needed in hospitals, care homes and many other places.
Uphill task
That experience showed how willing people were to collaborate. But it was an uphill task, not least because the government often seemed to be unaware that there actually was a textiles sector in Britain.
“People stopped going out to buy things, that’s the negative,” said podcast speaker Richard Jessup from Gerber Technology. “But actually, the big positive that came out of it was that the manufacturers that are in the UK really stepped up.” Key to this was making a local connection between supply and demand.
“We can’t just take what works in Asia and expect it to work here.”
At the outset, everyone seemed to assume that clothes could only be made in Asia. That’s not surprising given that the offshoring (as it’s called now) to Asia began back in the 1980s. It set the scene for a massive reduction in the price of clothing – and massive waste as well.
Over the decades since then the amount of clothes produced for the British market has rocketed – by 400 per cent, according to Scott Walton of Kornit Digital, a podcast participants. But as he pointed out, look more closely and the true costs are much higher.
“It’s important to understand the actual costs of goods sold, rather than the costs of goods made,” he said.
Along with cheapness came bulk orders and disposability. “30 per cent of what we put on the shelves today is never sold. Another 30 per cent is either heavily discounted or returned,” said Walton.
With the new focus on sustainability as well as on shorter supply chains, Britain is ideally placed to take advantage of new technologies that could see items of clothing produced locally in microfactories, with fabrics digitally printed on demand.
Gerber called on the textile industry to take a leaf out of Nissan’s book. The motor manufacturer set up in Sunderland with a network of suppliers within a 10-mile radius of the plant, enabling it to react swiftly to any issues that arise.
But it will take investment and innovation. “We can’t just take what works in Asia and expect it to work here,” he said. Gerber noted that many Portuguese factories were ahead of us, fuelled by EU grants that aren’t available to Britain that allow businesses access to the latest technologies.
“We need government investment here,” noted Mills. Yes. Indeed. And with Brexit, the government will not have the excuse of having to abide by EU state aid rules.